Example of Raft Foundation design:
The higher structural loads and low bearing capacity of soil demands for raft foundation design. The example of raft foundation design is discussed here in details.
Example: Design a raft foundation of a raft foundation shown below. Some of the design constrains required for raft foundation design are as,
Design Constants:
Unit weight of soil (Ξ³) = 18 KN/m3
Service Load (P) = 188190.67 kN
Service load includes the total axial forces applied from column, lift wall weight , and load from basement walls.
Grade of Concrete = M30
Grade of steel = Fe 500D
Bearing Capacity (q) = 150 KN/m2
Angle of Repose of soil (Γ) = 300
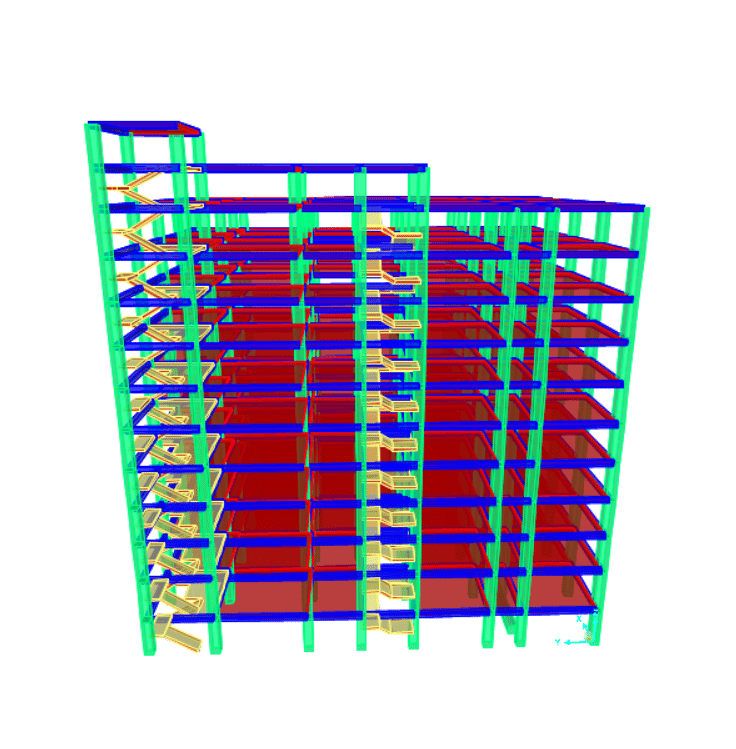
The raft foundation design with step wise procedure are as given:
As per IS 1893: 1 Cl 6.3.5.2 allowable bearing pressure in soil can be increased depending upon type of foundation thus bearing capacity of soil is increased by 50% assuming it will be Raft foundation
Then, q = 1.5Γ150 = 225 kN/m2 and applying factor of safety of 1.2, q = 187.5 kN/m2
Generally, the depth of raft foundation from ground level shall be not less than 1 m (IS 2950 Part 1, Cl. 4.3)
Df = ππ’/πΎπ Γ (1βπ ππΓ)2/(1+π ππΓ)2 = 187.5/18Γ(1βπ ππ30)2/(1+π ππ30)2 = 1.157 m > 1 m OK.
If the value was less than 1 m, the lower face of the designed footing shall have been placed at a level of 1 m below which soil is free from seasonal volumetric change.
The area of foundation required for safe transmission of load, assuming above reaction from superstructure is taken as non-eccentric surcharge to the soil, is given by:
Area of foundation required = Ξ£π+10% ππ Ξ£ππ = 1.1Γ188190.67 * 187.5 π2 = 1104 m2
Plinth area of the building = 1356.78 m2
Hence, % Area of required footing = (1104/1356.78)Γ100 = 81.37 % > 50%
Consider 500 mm projection for the raft having same shape of the superstructures along the building periphery for critical shear section consideration.
β΄ Area of Foundation provided = 1430.97 m2
Location of geometric C.G.: X = 15.24 m, Y = 21.265m
Calculation of Eccentricity:
Column | Service load | X | Y | F*X | F*Y |
ID | KN | m | m | ||
A1 | 3057.298 | 0 | 0 | 0 | 0 |
A2 | 3433.39067 | 0 | 7.16 | 0 | 24583.08 |
A3 | 3546.08333 | 0 | 10.32 | 0 | 36595.58 |
A4 | 4078.51267 | 0 | 17.48 | 0 | 71292.4 |
A5 | 4265.566 | 0 | 27.5 | 0 | 117303.1 |
A6 | 4845.374 | 0 | 36.23 | 0 | 175547.9 |
A7 | 2491.35333 | 0 | 42.53 | 0 | 105957.3 |
B1 | 4537.91333 | 7.62 | 0 | 34578.9 | 0 |
B2 | 5397.60667 | 7.62 | 7.16 | 41129.76 | 38646.86 |
B3 | 5567.01733 | 7.62 | 10.32 | 42420.67 | 57451.62 |
B4 | 6836.08933 | 7.62 | 17.48 | 52091 | 119494.8 |
B5 | 6945.63733 | 7.62 | 27.5 | 52925.76 | 191005 |
B6 | 7042.53333 | 7.62 | 36.23 | 53664.1 | 255151 |
B7 | 4210.06733 | 7.62 | 42.53 | 32080.71 | 179054.2 |
C1 | 4673.90933 | 15.24 | 0 | 71230.38 | 0 |
C2 | 5609.96333 | 15.24 | 7.16 | 85495.84 | 40167.34 |
C3 | 5733.08333 | 15.24 | 10.32 | 87372.19 | 59165.42 |
C4 | 6737.16867 | 15.24 | 17.48 | 102674.5 | 117765.7 |
C5 | 7416.846 | 15.24 | 27.5 | 113032.7 | 203963.3 |
C6 | 7247.21133 | 15.24 | 36.23 | 110447.5 | 262566.5 |
C7 | 4579.06267 | 15.24 | 42.53 | 69784.92 | 194747.5 |
D1 | 4547.16333 | 22.86 | 0 | 103948.2 | 0 |
D2 | 5485.98067 | 22.86 | 7.16 | 125409.5 | 39279.62 |
D3 | 5611.94533 | 22.86 | 10.32 | 128289.1 | 57915.28 |
D4 | 7946.608 | 22.86 | 17.48 | 181659.5 | 138906.7 |
D5 | 8692.12533 | 22.86 | 27.5 | 198702 | 239033.4 |
D6 | 7090.10933 | 22.86 | 36.23 | 162079.9 | 256874.7 |
D7 | 4454.27467 | 22.86 | 42.53 | 101824.7 | 189440.3 |
E1 | 3118.13467 | 30.48 | 0 | 95040.74 | 0 |
E2 | 3641.17867 | 30.48 | 7.16 | 110983.1 | 26070.84 |
E3 | 3718.392 | 30.48 | 10.32 | 113336.6 | 38373.81 |
E4 | 5271.26467 | 30.48 | 17.48 | 160668.1 | 92141.71 |
E5 | 5760.85733 | 30.48 | 27.5 | 175590.9 | 158423.6 |
E6 | 4714.16267 | 30.48 | 36.23 | 143687.7 | 170794.1 |
E7 | 3115.51933 | 30.48 | 42.53 | 94961.03 | 132503 |
A8 | 2641.38267 | 0 | 22.49 | 0 | 59404.7 |
Total | 184060.786 | 2845110 | 3849620 |
The total service load from the table and initially taken is different because the load of staircase and shear wall should also be taken for the area calculation.
XΜ = (Ξ£πΉπΓππ)/Ξ£π = 15.457 m
Θ²= (Ξ£πΉπΓππ)/Ξ£π = 20.915 m
Load Centroid (X, Y) = (15.457m, 20.915m)
ex = 15.457 β 15.24 = 0.217 m
ey = 21.265 β 20.915 = 0.35 m
Mx = P * ey = 188190.67 * 0.35 = 65866.74 KN-m
My = P * ex = 188190.67 * 0.207 = 40837.37 KN-m
Ixx = BD3/12 = 32.28 * 44.333 /12 = 234340 m4
Iyy = DB3/12 = 32.283 * 44.33 / 12 = 124256 m4
Soil Pressure at different Points (corner and edge) are as follows:
Column ID | P/A | Ixx | Iyy | X | Y | Mxx*Y /Ixx | Myy * X/Iyy | Soil pressure |
Corner A1 | 131.5 | 234340 | 124256 | -16.14 | -22.165 | -6.230 | -5.304 | 119.966 |
A2 | 131.5 | 234340 | 124256 | -16.14 | -14.105 | -3.965 | -5.304 | 122.231 |
A3 | 131.5 | 234340 | 124256 | -16.14 | -10.945 | -3.076 | -5.304 | 123.119 |
A4 | 131.5 | 234340 | 124256 | -16.14 | -3.785 | -1.064 | -5.304 | 125.132 |
A5 | 131.5 | 234340 | 124256 | -16.14 | 6.235 | 1.752 | -5.304 | 127.948 |
A6 | 131.5 | 234340 | 124256 | -16.14 | 14.965 | 4.206 | -5.304 | 130.402 |
Corner A7 | 131.5 | 234340 | 124256 | -16.14 | 22.165 | 6.230 | -5.304 | 132.425 |
Corner E1 | 131.5 | 234340 | 124256 | 16.14 | -22.165 | -6.230 | 5.304 | 130.575 |
E2 | 131.5 | 234340 | 124256 | 16.14 | -14.105 | -3.965 | 5.304 | 132.840 |
E3 | 131.5 | 234340 | 124256 | 16.14 | -10.945 | -3.076 | 5.304 | 133.728 |
E4 | 131.5 | 234340 | 124256 | 16.14 | -3.785 | -1.064 | 5.304 | 135.741 |
E5 | 131.5 | 234340 | 124256 | 16.14 | 6.235 | 1.752 | 5.304 | 138.557 |
E6 | 131.5 | 234340 | 124256 | 16.14 | 14.965 | 4.206 | 5.304 | 141.011 |
Corner E7 | 131.5 | 234340 | 124256 | 16.14 | 22.165 | 6.230 | 5.304 | 143.034 |
B1 | 131.5 | 234340 | 124256 | -7.62 | -22.165 | -6.230 | -2.504 | 122.766 |
C1 | 131.5 | 234340 | 124256 | 0 | -22.165 | -6.230 | 0.000 | 125.270 |
D1 | 131.5 | 234340 | 124256 | 7.62 | -22.165 | -6.230 | 2.504 | 127.774 |
B7 | 131.5 | 234340 | 124256 | -7.62 | 22.165 | 6.230 | -2.504 | 135.226 |
C7 | 131.5 | 234340 | 124256 | 0 | 22.165 | 6.230 | 0.000 | 137.730 |
D7 | 131.5 | 234340 | 124256 | 7.62 | 22.165 | 6.230 | 2.504 | 140.234 |
Hence maximum downward stress (140.234 kN/m2) is less than safe bearing capacity (187.5 kN/m2) so OK.
In X-direction raft is divided in seven strips that is into 5 equivalent beam, the beam with the respective soil pressure and moment are as follows.
Bending moment is obtained by coefficient (1/12) and βLβ as center to center distance, from IS 456 Cl. 22.5.1
+M = -M = wl2/12
Beams | Strip width | Length L | Coeff. | Soil pressure | Equivalent soil pressure | Soil pressure per strip KN/m2 |
A-A | 4.71 | 10.02 | 1/12 | 132.425 | 132.425 | 1107.960 |
B-B | 7.62 | 10.02 | 1/12 | 135.225 | 133.825 | 1119.674 |
C-C | 7.62 | 10.02 | 1/12 | 137.73 | 136.4775 | 1141.866 |
D-D | 7.62 | 10.02 | 1/12 | 140.23 | 138.98 | 1162.804 |
E-E | 4.71 | 10.02 | 1/12 | 143.03 | 141.63 | 1184.976 |
Maximum | 1184.970 |
In the Y-direction the raft is divided into 7 strips i.e. into seven equivalent beams.
Beams | Strip width | Length L | Coeff. | Soil pressure | Equivalent soil pressure | Soil pressure per strip KN/m2 |
1 | 4.48 | 7.62 | 1/12 | 130.57 | 130.57 | 631.79 |
2 | 5.16 | 7.62 | 1/12 | 132.84 | 131.71 | 637.28 |
3 | 5.16 | 7.62 | 1/12 | 133.73 | 133.28 | 644.92 |
4 | 8.59 | 7.62 | 1/12 | 135.74 | 134.73 | 651.94 |
5 | 9.375 | 7.62 | 1/12 | 138.56 | 137.15 | 663.62 |
6 | 7.52 | 7.62 | 1/12 | 141.01 | 139.78 | 676.37 |
7 | 4.05 | 7.62 | 1/12 | 143.03 | 142.02 | 687.20 |
maximum | 687 .20 |
Therefore, maximum moment is 1184.97 kNm/m per strip.
Calculation of Depth of Foundation:
i. Calculation of Depth from Moment Criterion (IS 456 : 2000, ANNEX G 1.1):
Mu = 0.133 fck b d2 [for fe500]
1184.97 * 106 = 0.133 * 30 * 1000 * d2
d = 545 mm
ii. Calculation of Depth from Two Way Shear:
Depth of raft will govern by two-way shear at one of the exterior column. In case, location of critical shear is not obvious it may be necessary to check all locations. When shear reinforcement is not provided, the calculated shear stress at critical section shall not exceed KsΓΟc. i.e. Οv β€ KsΓΟc. (IS 456 : 2000, Cl. 31.6.3.1)
Where,
Ks = (0.5 + Ξ²c) but not greater than 1, Ξ²c being the ration of short side to long side of the column/capital; and
Οc = 0.25 βπππ in limit state method of design.
Here, Ξ²c = 1
Ks = 1+0.5 = 1.5 > 1
Hence, Ks = 1
Shear strength of concrete (Οc) = 0.25Γβ30 = 1.37 N/mm2
For column D5
Factored Column Load = 13038.19 kN
Perimeter (po) = 4 (d + 800)
The nominal shear stress in flat slabs shall be taken as V/(poΓd) where V is the shear force due to design, P0 is the periphery of the critical section and d is the effective depth of the slab. (IS 456 : 2000, Cl. 31.6.2.1)
ππ£=ππ’/(ππΓπ)
1.37 = 13038.19Γ103/[4(π+540)Γπ]
d = 1193.87 mm
For corner column E7
Factored Column Load = 4677.2 kN
Perimeter po = 2Γ(0.5d + 800 + 500 + 0.5d + 800+500) = 2Γ(d + 2600)
ππ£=ππ’/(ππΓπ)=4677.2*103/ 2(π+2600)Γπ
ππ,1.37=4677.2Γ103/ [2(π+2600)Γπ]
Hence d = 543.33 mm
Hence, the thickness of raft foundation design is governed by two-way shear.
Adopt effective Depth (d) = 1200 mm
Adopt effective cover of 65 mm (IS456: 2000, Cl. 26.4.2.2)
Overall Depth = 1200 + 65= 1265 mm
Reinforcement calculation:
In shorter Direction
We have from (IS 456 : 2000, Annex G 1.1)
BM = 0.87ΓfyΓAstΓ(d β ππ¦Γπ΄π π‘/πππΓπ)
Or, 687Γ106 = 0.87Γ500ΓAstΓ(1200 β 500Γπ΄π π‘/ 30Γ1000)
Solving we get,
Ast = 1341.07 mm2
The mild steel reinforcement in either direction in slab shall not be less than 0.15% of the total cross-sectional area. However this value can be reduced to 0.12% when high strength deformed bar or welded wire fabric are used. (IS 456 : 2000, Cl. 26.5.2.1)
Minimum reinforcement in slab = 0.12%Γ1000Γ1265 = 1518 mm2
i.e. Ast, required < Ast, Min.
So, Ast, required = 1518 mm2
Using 16 mm Γ bars,
Spacing of Bar (Sv) = π΄π/π΄π π‘Γ1000=201.062/1518Γ1000=132.45 ππ
Hence, provide 16 mm Γ Bars @ 120 mm C/C in Shorter direction.
Therefore, Ast, Provided = (201.062/120)Γ1000 = 1675.52 mm2
In Longer Direction:
Adopt effective depth = 1200 β 16 = 1184 mm
Reinforcement in longer direction is given by:
BM = 0.87ΓfyΓAstΓ(d β ππ¦Γπ΄π π‘/πππΓπ)
Or, 1184.97Γ106 = 0.87Γ500ΓAstΓ(1184 β 500Γπ΄π π‘/30Γ1000)
Solving we get Ast = 2380.50 mm2
Minimum reinforcement in slab = 0.12%Γ1265Γ1000 = 1518 mm2
i.e. Ast required > AstMin. OK.
Using 16 mm Γ bars,
Spacing of Bar (Sv) = π΄π/π΄π π‘Γ1000=201.062/2380.50Γ1000= 84.46 ππ
Hence, Provide 16 mm Γ @ 80 mm C/C in Longer direction.
Therefore, Ast provided = (201.062/80)Γ1000 = 2513.275 mm2
Check for Development Length:
Bond Stress (πππ)=1.4 π/ππ2, For M30 Concrete. This value can be increased by 60% for Tor Steel. (IS 456 : 2000, Cl. 26.2.1.1)
The development length (Ld) is given by (IS 456 : 2000, Cl. 26.2.1)
πΏπ=β Γππ /4Γπππ= β Γ0.87Γ500/(4Γ1.6Γ1.6)=42.48β
Ld = 42.48Γ16 = 679.68 mm
πΏπβ€ 1.3Γπ1/π+ππ (IS 456 : 2000, Cl. 26.2.1)
lo = Effective depth or 12β , Whichever is greater.
πΏπβ€ 1.3Γ1184.97Γ106 /4677.2Γ1000+1200=1529.08 ππ OK.
Load Transfer from Column to footing:
Nominal bearing stress in column concrete (Οbr) = Pu/Ac
= (13038.19Γ1000)/(800Γ800) = 20.37 N/mm2
Allowable bearing stress = 0.45Γfck = 0.45Γ30 = 13.5 N/mm2 (IS 456: 2000, Cl. 34.4)
If the permissible bearing stress on the concrete within the supporting or supported members exceeded, reinforcement shall be provided for developed surplus force by dowels. (IS 456: 2000, Cl. 34.4.1)
Dowel of at least 0.5% of the cross-sectional area of the supported column and a minimum of four bars shall be provided. Diameter of the Dowels shall not exceed the diameter of column bar by more than 3 mm. (IS 456 : 2000, Cl. 34.4.1)
Area of Dowels Bar = 0.5%Γ800Γ800 = 3200 mm2
Provide 28 mm β as Dowel bar.
Development length for dowel bar = β Γππ /4Γπππ= 28Γ0.87Γ500/4Γ1.6Γ1.6=1189.45 ππ
Use 6 β 28 mm β Bars as Dowel Bar, then As, provided = 6ΓPIΓ282/4 = 3694.5 mm2 > 3200 mm2
Also read: